从流程管理层面推进精益管理
日期:2016-10-21 / 人气: / 来源:www.biglss.com / 热门标签:
欢迎您访问博革咨询官网!博革咨询是中国首家整合精益生产/六西格玛/流程再造的咨询公司,专注于提供 精益生产、6S现场管理、TPM设备管理、精益工厂布局、专业目视化、精益供应链、精益研发、六西格玛管理等综合性问题解决方案并负责落地实施。
全国咨询热线:021-62373515、157-2153-3189
我们承诺:见效快、易复制,目标必对赌!
l 消除浪费
生产活动过程中不直接创造价值的活动全部可以定义为浪费,精益变革活动推进是从消除浪费角度切入,加强增值部分在整个运营中占比的过程。根据有关资料的调查,一般认为一家企业运营过程中95%以上的活动都是浪费。如下图,若我们把改善切入点放在怎样提升增值占比时,就算改善辅导达到100%,其整体的效果来讲,增值部分在整个运营中的占比只有10%。若反过来,我们把切入点放在消除浪费上,我们就会发现,就算改善幅度只有50%,其改善成果来看时,增值部分在整个运营中的占比就52.5%。
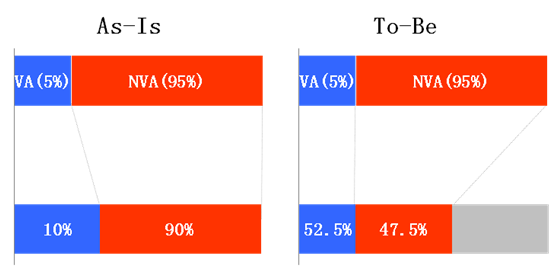
消除浪费有效性示意图
浪费的区分方法中最为常见也是最普遍的是以浪费的形态划分的丰田7大浪费,也就是等待的浪费、加工本身的浪费、动作浪费、库存浪费、制造不良的浪费、生产过剩的浪费、搬运的浪费。
l 建立流动运营系统
“户枢不蠹、流水不腐”,创造价值的各个步骤必须要全面流动起来,停滞就是一种浪费的表现。停滞代表的是现场的库存、现场的不良品、未发货的成品、等待使用的原材料等等,这种停滞物品的多少直接与产品的交付周期长短有关联、直接与企业的现金流管理有关联。
影响企业运营发生停滞的主要原因有生产批量的大小和运营过程中存在的瓶颈。那么让系统流动起来,也就是发现瓶颈、消除瓶颈并把生产批量不断缩小,直至实现单件流的过程。如下图所示,水流足够大时我们是无法看到水底下的暗礁隐患,这种隐患我们虽然看不到,但他们是确确实实存在的,也是在影响着整个水流的流动速度和流动量的。这与企业运营基本一致,当生产批量较大时,企业内部运营过程中发生的设备故障、物料损耗、产品不良、返工以及生产周期时间过长等问题都是无法感知到的,因为虽然生产成本居高不下,但很多情况下以大量的库存的制造成本为代价,还是可以按时出货、满足客户的需求的。
解决这种逆境的方法中最有效的方法之一,就是不断的降低水面,让水下的暗礁一点一点的显露出来,而我们呢,发现一个暗礁,就处理一个,然后继续降低水面,直到看不到一丁点暗礁为止。把上述方法应用在生产过程中,那就是不断减少生产批量,达到均衡化生产的目的。为了达到这种变革目的持续要改进如快速换模、不良率降低、标准化工作推进以生产效率提升等一系列工作。在这种操作模式下,如果准备工作不充分,很容易发生在变革初期相应的现场管理指标变差的现象,在这种情况下我们管理团队必须要正视这种问题的同时,也要从管理角度上设置其他精益管理指标进行管控,因为精益变革初期虽然一些传统指标变差了,但更为积极的是肯定有很多精益指标变好了,如在制品库存的金额、产品交货周期、库存周转率、快速响应速度等等。
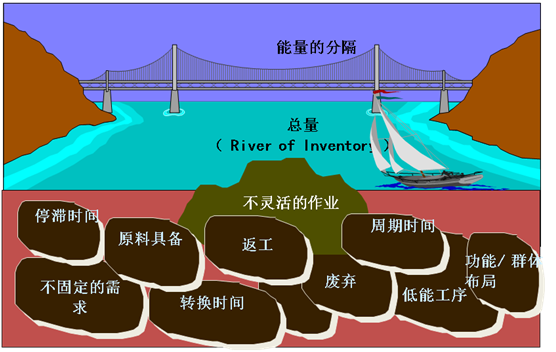
企业运营瓶颈图示
l 按需求拉动,避免过量生产,实现准时化生产(JIT)
推动式生产模式可以说是传统生产系统下造成大量库存和浪费的主要原因。精益变革过程中,按需求拉动式生产是实现准时化生产(JIT)的技术承载。
需求拉动式生产方式是在储备一定的成品和工序在制品的条件下,根据需求由后向前层层拉动每道工序生产,从而达到按时按量提供所需产品。通过需求拉动式生产来促进企业各个环节不断改善从而达到精益生产的目标,是企业实施精益生产的必经之路。
需求拉动式生产以准时化生产为核心,以降低成本、持续改善和提高为目标,通过需求拉动式组织方式的实现来逐步消除无效生产,压缩库存储备,降低生产成本,更加及时和有效地满足市场需求的变化,不断改进和完善系统运行方式,从而逐步达到精益生产的要求。
准时化生产指的是在正确的时间、以正确的方式、按正确的路线,把正确的物料,送到正确的地点、每次都刚好及时。
需求拉动式生产方式是立足于企业的实际,在质量控制达标是3西格玛标准的情况下,推进初期允许设立有少量安全的库存和在制品储备。实现拉动生产模式最有效的方法之一是应用KANBAN系统。通过KANBAN的传递,替代原有计划模式下的排产计划,实现拉动式生产。有3种不同的拉动生产系统模式,其一是补充式拉动系统、其二是顺序式拉动系统。
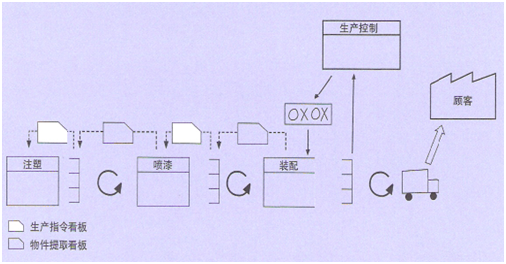
不充式拉动系统
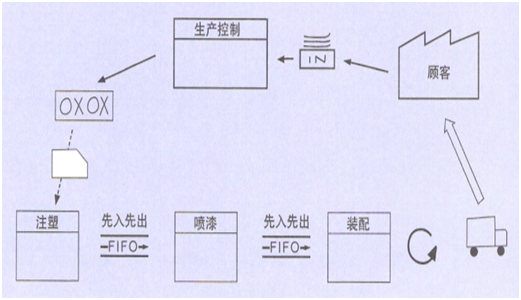
顺序式拉动系统
l 不断设定标准并改进标准
设定标准的最主要目的是减少变异或流程的波动。无论我们采用了KANBAN拉动生产模式也好,流动生产系统也好,如果没有明确的标准其落实效果肯定不能达到导入这种精益系统的预期。在精益变革过程中我们要持续进行否定现在的流程、改善程更为优秀的流程、针对改善成果设定标准、按照标准进行操作的循环工作。
在精益变革中我们要设定很多标准,其中最为重要的是标准作业。标准作业是针对以人的动作为中心的重复性工作设定的标准,它包括T.T、作业顺序、标准在库。标准作业中设定是以现场员工的实际参与为基础,明确规定了工位描述、动作步骤、图示图片、物料描述、工具描述、审批更改、安全要点、质量检查、关键质量、时间要素。

标准作业模板
在实际变革过程中很多推进人员最为头疼的事情之一是改善成果不能维持,其主要的原因是,所制定的操作方法或改善手法,现场操作工没有完全按照标准执行下去。标准和实际操作差异越大,改善难度就越高。在精益变革初期,我们必须要花很多时间对现有的工作进行标准化,并定期进行现场审核,保证标准化执行率逐步提升。在这个阶段无论标准化的内容是否恰当,我们都应该把重点放在他们执行的一致性上。为了实现这点,在推进标准化初期,一定是以现场员工或班组长为中心推进标准化工作。
l 自主管理、追求零缺陷 (自働化)
精益变革中我们不断最寻的是动态平衡,是速度和质量的平衡。就像下图中所展现,精益生产的2大支柱是JIT和自働化。为了实现准时化生产,在生产运营各个环节我们所采取的措施都是怎样提升速度及效率;同理为了实现自働化我们要通过自主管理、停线机制、安灯、简易自动化等措施保证产品的质量。
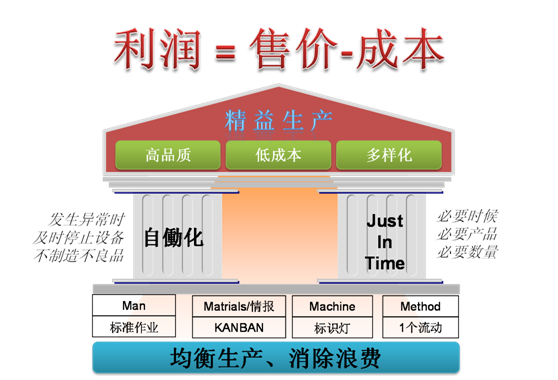
精益生产屋
一般来说,自主管理是主要通过员工的自我约束,自我控制,自我发现问题,自我分析问题,自我解决问题,以变被动管理为主动管理,进而自我提高,自我创新,自我超越,推动组织不断发展与前进的管理方式。精益变革中指的自主管理与上述内容相比应该说更为狭隘,主要指的是质量管理领域上的自主性,具体指的是自己主动检查所生产工序之品质、自己主动检查负责工序来料之品质、自己主动检查所负责工序设备状况。
停线机制是为了防止不良品流入到后工序,在生产活动过程中发现不良品时有一线员工主导决定停线,并促使相关人员改进的一种管理手法。为了更好的实现停线机制现场经常应用的是安灯设备,它可以起到以可视化的方式第一时间把现场问题通报给相关人员的作用。停线机制很简单,但真正实施到位的企业不多,最重要的原因是没有做好可真正实施停线机制必须的工作。推进停线机制时必须要做好以下几点工作
1) 明确过程质量控制基准,要做到生产系统和质量系统人员的标准的一致性;
2) 分层管理基准明确。根据问题的类型和复杂度,设定不同层级的人员对应;
3) 现场问题解决台账管理。当现场发生问题时,发生最多的是现场来了很多人,但没有办法解决现场问题或没有人愿意拍板确定措施。如果一线班组长、工艺工程师、品质工程师等不同层级人员,根据以往处理问题的数据整理了一份解决问题台账,那么上述问题就可以迎刃而解。
4) 停线点设计和缓冲区设计等
停线机制的运营直接与当前生产任务的达成相关,这也是停线机制很难落实下去的原因。虽然长远来看,停线机制肯定对企业发展有利,但短期来看也确实是影响每日的生产。那么在推进停线机制过程中我们也要重点考虑怎样降低他对生产的影响。普遍采用的方式是在生产工艺流程中,根据CTQ(关键质量特性)工位、特殊工位以安全法规工位等重点工位为主设定停线点,并在每个停线点设定一定数量的缓冲库存量,以此来确保对生产的直接影响。这种缓冲库存的设计是占时的,我们可以根据精益变革的进程,逐步减少缓冲库存量,以此达到持续变革的最终目的。
l 全流程整体优化
局部的最佳,不代表整体效果最优化。精益变革过程中我们一定要以客户的需求为导向,以宏观角度发现问题、改善问题,力求全流程整体的最优化。
如下图所示,在产品研发过程中每个研发小组站在部门的角度所设计的产品都最优秀的,但等到把4个组开发出来的产品组合在一起时,我们发现他与客户的期望相差甚远。

局部最佳和整体优化
作者:博革咨询