八大浪费之员工提案的重要性
欢迎您访问博革咨询官网!博革咨询是中国首家整合精益生产/六西格玛/流程再造的咨询公司,专注于提供 精益生产、6S现场管理、TPM设备管理、精益工厂布局、专业目视化、精益供应链、精益研发、六西格玛管理等综合性问题解决方案并负责落地实施。
全国咨询热线:021-62373515、157-2153-3189
我们承诺:见效快、易复制,目标必对赌!
TPS(丰田制造系统)讲七大浪费,美国人通过研究提出第八大浪费——员工智慧的浪费;毛主席抗战时期也曾说过“人民的力量是无穷的,人民的智慧是无限的”。因此,企业管理者若能充分调动公司全员积极思考,为公司的发展出主意、想办法,企业将取得巨大的成功;实施这一战略的有效管理工具就是基于正激励的“合理化建议”和“现场改善”的成功实施。
博革咨询通过培训、宣贯和建立正激励机制,发动企业全体员工提出企业各个方面的改进意见并实施,企业管理者不必顾虑奖金的发放,因为合理化建议的实施是一个“赚钱”的项目,激励奖的发放也是以实施后的效果评价为依据的。
现场的定义就是增值地方,是企业经营管理活动的基础。现场是精益生产的细胞,它每一个现场体现了精益生产的所有基因信息。一个精益的现场,它会让您感觉生产井然有序、信息一目了然、生产人员和管理人员沟通有效。
现场改善是通用汽车等国际知名企业普遍采用的一种现场管理方法。它与传统意义上的现场改善方法不同:它始于现场,终于现场,而不是从办公室做一个规划,然后由现场人员实施;而且它遵循一个点一个点的改善,逐步推进,不搞运动。一个典型的现场改善包括:我们培训员工通过现场寻找浪费、确认问题并形成问题清单(Open Issues)、开展改善活动、成果汇报、庆祝等五个步骤实施改善。
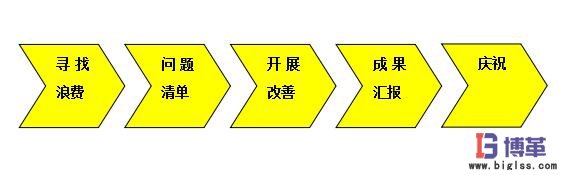
Ⅱ)、形成问题清单:只有现场才是增值的地方,也只有问题才使管理人员有存在的意义,因此现场改善改变了过去的那种坐在办公室里做计划的习惯,使现场的问题直接就变成了改进的计划落实到具体的人员限时完成,保证了计划的有效性和严肃性。
Ⅲ)、开展改善:参与改善的区域不能太大,否则问题将超出短期改善的范畴,牵扯出很多系统性的(一下无法解决)问题。我们应针对能在短期改进的问题,通过各种团体思维方法,结合精益生产的原则完成改善。
Ⅳ)、成果汇报:对改善的成果,通过各种途径进行PDCA循环,其中成果汇报就是其中一个。让公司的领导知道改进的成果,并对成果进行总结。
Ⅴ)、庆祝:目的是为了鼓励士气和更好的巩固改善的成果。
生产方式的根本是以最少的人员和少量的设备,少量地使用材料, 使得 在所需要的时间内,按照所需要的数量生产所需要的产品. 为了实现这个根本, 需要进行三个方面的改善 :
1 生产现场的改善。
生产现场的改善是由生产第一线的现场监督人员来实施改善技法。将必须要改善的生产·管理·技术方式及改善推进组织的各个项目和改善重点,按照实施顺序整理出来,进行级别评估。最理想的是实施的改善能够提高各个项目整体水平。
2 生产准备的改善。
生产准备的改善是应当由开发、生产、制造、品质管理及管理技术人员为主实施的改善技法。 生产准备是指:
A/新产品的计划·设计阶段所设定的设计品质。
B/所需要的产量 。
C/成本 。
3 生产管理的改善 。
生产管理的改善应当是从事管理工作的管理者实施的改善技法。 经常听到这样的话,“制造现场的改善活动虽有进展, 但改善效果没有充分地反映到经营上来”、或是“做了一个使用电脑的生产管理系统,却没得到充分利用”。这说明构筑一个管理系统,没有硬件(制造现场)的生产方式的改善是行不通的。
作者:博革咨询