德国大众的精益生产体系发展过程
日期:2017-02-21 / 人气: / 来源:www.biglss.com / 热门标签: 德国大众
欢迎您访问博革咨询官网!博革咨询是中国首家整合精益生产/六西格玛/流程再造的咨询公司,专注于提供 精益生产、6S现场管理、TPM设备管理、精益工厂布局、专业目视化、精益供应链、精益研发、六西格玛管理等综合性问题解决方案并负责落地实施。
全国咨询热线:021-62373515、157-2153-3189
我们承诺:见效快、易复制,目标必对赌!
德国大众在把学到的精益生产体系结合企业自身特点进行调整,形成了自己的精益体系,他们通过一系列的方法来应用并推广这套体系。那么德国大众的精益生产体系发展过程是怎样的呢?博革咨询为大家总结了如下几个方面:
(1)精益生产的发展
丰田生产方式萌芽于上个世纪二战后,当时日本经济还没有从战争后复苏,当时的丰田公司正面临着破产的危机。在这样的时代背景下,丰田公司提出了“准时制”的思想,经过20年的改造、创新和发展,逐渐形成丰田生产方式。1990年麻省理工学院沃麦克教授等人撰写了《精益生产方式———改变世界的机器》一书,对日本企业取得的成功经验进行总结,提出了精益生产的概念。书中在做了大量的调查和对比后,认为日本丰田汽车公司的生产方式是最适合现代制造业的一种生产组织管理方式,称之为精益生产方式。
精益生产作为一种以顾客需求为导向,多品种、大批量、高质量、低消耗、快速反应市场的生产方式,不但给企业带来了巨大效益,而且降低库存、提高品质、缩短开发与生产周期、减少用工、加快了对市场的反应速度,同时通过转变员工的管理理念、创新能力和团队协作精神等,给企业带来无形效益。
(2)德国大众精益生产的学习阶段
随着世界汽车产业的成熟和兼并重组步伐的加快,世界各汽车厂家在技术方面的差异在逐渐缩小,企业已无法靠已往的技术优势来保持竞争力,因此,各大汽车公司都在开发和应用先进的生产现场管理体系,以提高生产效率,降低生产成本,并藉此保持企业的竞争力。
丰田公司的精益生产方式在实际应用中获得了很好的效果,在上世纪被各行业广泛地学习,汽车行业更是形成了一股学习丰田的浪潮。德国大众高层也意识到精益体系对于企业的生存发展具有重大意义,因此以皮耶希为代表的大众人开始学习日本先进的精益生产方式,调研分析丰田的精益体系。
(3)德国大众精益生产体系的形成
学来的精益体系不能生搬硬套,必须结合企业自身的战略和文化进行调整。因此,上个世纪90年代,在学习了精益体系之后,德国大众结合自己企业的特点,开发出了适应德国大众文化的一整套体系,并且首先在奥迪公司进行试点,然后经过加工提炼,形成了适合大众全集团的工作体系,叫做大众生产系统。大众生产系统是以九要素的推行方式来开展的,九要素包括:班组工作、过程质量控制、全面效率维修、目标管理、物料管理、工位组织、目视管理、标准化操作及改进工作。
2005年德国大众在原有基础上,开发了KVP-Kaskade这种体系推进方式,其中Kaskade的字面本意是瀑布或像瀑布一样流下,KVP-Kaskade寓意为:持续不断的、气势磅礴的、全员参与的改进。
2007年,在德国大众提出的2018战略基础上,将原有大众生产系统加以优化,优化后的大众生产系统由一个基础和四个原则所构成的。基础包含均衡生产、持续改进消除浪费、标准化、工作组织及环境保护。节拍原则是以客户需求为节拍;流动原则是要减少流程时间;拉动原则代表拉动式生产流程;完美原则追求零缺陷。这套大众生产系统基于KVP-Kaskade的五个波次来推行,具体的五个波次是:
KVP-Kaskade的五个波次:
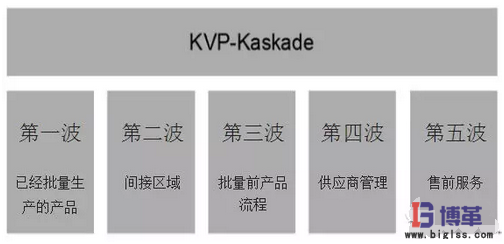
第一波主要针对已经批量生产的产品,在直接生产区域进行优化。目前已经分阶段地在德国大众全球的各个生产基地逐步开展;
第二波是在间接区域进行优化,例如在职能部门等;
第三波是针对批量生产前的产品流程进行优化;
第四波针对供应商管理进行优化;
第五波针对售前服务进行优化。上述的这五个波次之间相互独立,并无先后顺序,公司可以根据不同阶段的战略规划来选择相应的波次进行精益优化工作。
作者:博革咨询