走出“0“库存的误区
日期:2016-10-20 / 人气: / 来源:www.biglss.com / 热门标签: TPS 0库存 精益生产
欢迎您访问博革咨询官网!博革咨询是中国首家整合精益生产/六西格玛/流程再造的咨询公司,专注于提供 精益生产、6S现场管理、TPM设备管理、精益工厂布局、专业目视化、精益供应链、精益研发、六西格玛管理等综合性问题解决方案并负责落地实施。
全国咨询热线:021-62373515、157-2153-3189
我们承诺:见效快、易复制,目标必对赌!
目标“0”库存
就像大家所熟知的,精益生产是由日本丰田公司创造并建立起来、在世界范围内予以推行的;习惯称呼为TPS(丰田生产模式)。这套体系的建立,源于对经济危机的应对,根本上说就是为了生存。那么拿生存的需求对比利润的追求而言,前者对待周遭要苛刻的多,可谓是竭尽所能、算无遗策,这也是TPS为什么目标指向“0库存”的原因。
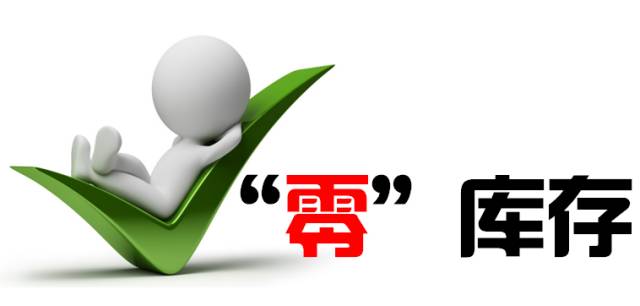
但,要明白的是,“0库存”是一个目标、一个方向,而不是一个手段,有时候它甚至只是一个愿望。我们要实事求是、根据企业行业的不同、规模的大小、供应链的评级高低和完善程度等,具体问题具体分析、对待,而不是以偏概全,把“0库存”作为比之所有企业而皆准的手段,否则,效果适得其反,带来的不是结果,而是后果。
笔者曾带领团队做过一家体育用品公司的项目,这家公司的交期存在严重的问题,均值已经超过了三个月;表面看,交期长似乎不是什么坏现象,只要客户认可就行;恰恰相反,这应该说明订单充足、生产无虞、值得庆贺才对;而事实是,这些订单本可以及时交货、却由于生产不顺畅、一推再推、一拖再拖、弄的客户怨声载道、订单时有取消,跟单员离职率高、频换更换、和生产人员关系相处的也非常紧张,众说纷纭,形成了一个恶性循环的怪圈。
后经过调研、诊断,发现事情远没有其所表现的那么复杂,该公司的工序为:下料、冲孔、钻孔、焊接、打磨、酸洗、喷涂、组装、包装;下料是首道工序,下料后根据产品的不同可能进行冲孔、钻孔、焊接;也可能冲孔后焊接、打磨或直接打磨;或者钻孔后焊接、打磨或直接打磨;再或者直接焊接、打磨等;这就涉及到首道下料工序下好的料的数量管理和去向控制问题。
该公司老板外贸出身、理念先进、追求的是国际化的工厂,要求现场绝对不能有过剩的库存、更不允许有专门设立的半成品仓库。实事求是的讲,这种想法、这种理念是好的、值得肯定,但能不能运用、运用的如何才是检验的标准吧。就上面的事情而言,他要求的不设专门半成品仓库倒是做到啦,而不准有多余的库存却恰恰相反、工位旁、过道内、墙边、墙角、甚至生产车间外放车子的棚子里都堆满了半成品。
为什么会造成这样的现象?
第一,首道工序对应后面多道工序、并且根据产品的不同,对应关系还不停的发生变化;这就从客观上要求要备一个生产周期的库存。
第二,多为非常规产品、切换频繁,产品一旦切换、后续可能永不生产,这也表明:1、基本没有通用配件、一旦缺料(品质不良造成的缺料、数量确认错误造成的缺料等),必须停机待料;2、一旦该批次产品生产完成、多余的配件几乎无再用的可能,只能作废。
第三,基于上述两点,员工为了尽可能的完成生产任务,会自发的生产备料,由于无处可放,所以到处乱塞,这也导致了有些料明明知道已生产出来,后道用的时候却找不到,只能重新生产,后续不用的时候又找到啦,由于该订单已经停止,此料无型号可用,又不敢废弃,只能乱塞,弄的现场越来越乱,恶性循环。
由鉴于此,就设立中间库存的想法与该公司老板做了沟通,起初满是抵触,这可以理解。后续还是这样做了,设立下料工序半成品仓库,纳入正常的仓库管理、导入地址系统、目视管理、最大最小安全库存设定、先进先出等,专人负责,由PMC统一管理。效果非常明显。
首先,工厂清理出数量庞大的无用配件库存、现场作业环境有了质的改观,同时,也从根本上斩断了这种多余配件产生的环境;
其次,也是最重要的,经过一个多月的控制、其最长生产周期的产品在七天零不到三个小时的时间内便可完成;经过五个多月的运营,其交货周期完全可控制在一个月之内(30天),完全能够兑现对客户的承诺。
总结:
“0”库存是我们的目标、我们要在基于综合效益的考虑下尽可能的去降低库存、去接近这个目标,但、不可盲目的作为一种手段、一种工具试图去改造所有。要知其然也要知其所以然!
作者:博革咨询